Pick and Pack Order
Fulfillment at IDS
IDS Pick and Pack Order Fulfillment Services
The need for pick-and-pack order fulfillment services grows exponentially in today’s retail world, where eCommerce is increasingly relied upon as a primary market channel. At IDS, we focus on our clients and their brands with processes and procedures designed around your business and products. Our capabilities, flexibility, and process-driven approach enable our clients to aggressively pursue their own marketing, branding, and sales opportunities while knowing their efforts are backed up with a responsive and successful experience from customers placing an order all the way through to receiving and opening their packages. We provide a complete and scalable platform to align with our clients’ changing needs while continuing to meet the KPIs most important to your business.
What is Pick and Pack Fulfillment?
Pick and pack fulfillment is a business logistics subtask of order processing that involves picking individual items from the shelves of a warehouse, packing them, and then shipping them to the consumer. However, the end-to-end process consists of several steps. It begins when a consumer places an order, which these days is primarily through an online store. When the customer places the order, it will be routed to whatever order fulfillment center is responsible for filling the order and getting it sent to the customer. Some companies handle all this in-house, but many have outsourced order fulfillment to third-party logistics partners who manage it for them.
The warehouse management system (WMS) generates a new order request and a packing slip, which is then assigned to a warehouse worker (a picker) who will retrieve the ordered item(s) from wherever they are in the warehouse. Once the picker has picked the ordered item(s), they will deliver them to the nearest packing station, where another warehouse worker (a packer) will select the appropriate packaging materials and pack up the order. Then, the package must have the correct shipping label applied to it, which can vary by shipping carrier, and off it goes. Given the constant pressure from consumers to get free shipping, making the pick-and-pack process as efficient as possible to control costs is critical.
Pick Methods for Order Fulfillment
The picking part of the process can be done using several different methods. IDS utilizes various methods based on which would be the most efficient for both your time and money while ensuring maximum accuracy in delivery. Here are different picking methods:
The Benefits of Outsourcing Pick and Pack Order Fulfillment
When most businesses are first starting out, they can easily handle order fulfillment in-house. Over time, however, if the business grows significantly, there will likely come a time when it realizes it no longer has the capacity or resources to handle order fulfillment in-house. This is when outsourcing to a third-party logistics (3PL) provider makes sense. In some cases, even after outsourcing, a business might grow or change enough that it outstrips the capacity of its first 3PL partner and must switch to a different one to meet its needs. Both scenarios include some telltale pain points indicating it’s time to make a change, including some or all of the following:
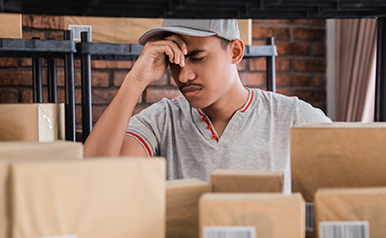
Shipping delays
Prompt shipping is crucial for customer satisfaction, and delays can significantly harm your company’s reputation and customer retention.
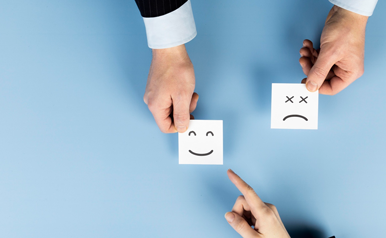
Customer Complaints
about shipments can lead to lost customers and negative reviews, impacting your business’s reputation and sales.
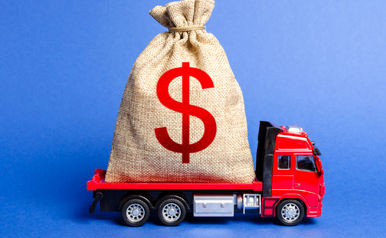
Shipping delays
Prompt shipping is crucial for customer satisfaction, and delays can significantly harm your company’s reputation and customer retention.
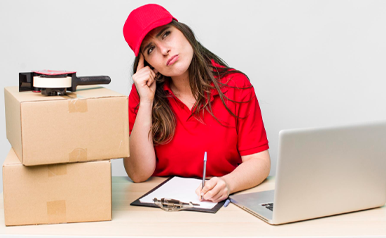
Inventory management issues
Efficient inventory management is fundamental for avoiding overstock or stockout situations, ensuring customer satisfaction and optimal operational efficiency.
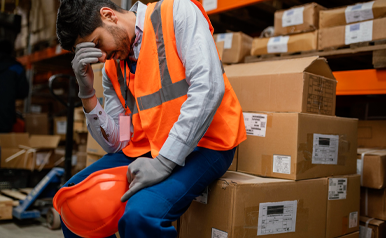
Limited storage space
Insufficient storage space can hinder business expansion and the ability to meet customer demand, limiting revenue potential.
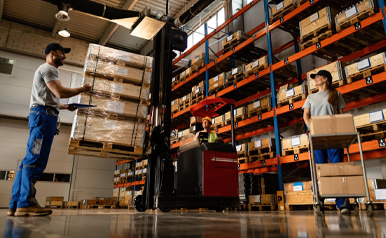
Inefficient fulfillment processes
Inefficiencies in fulfillment can lead to errors, delays, and increased costs, impacting both customer satisfaction and operational profitability.
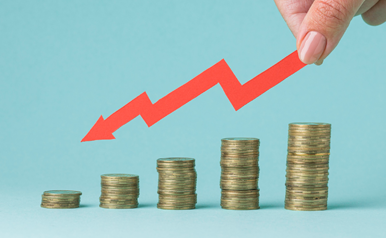
Limited capital
Lack of funds can prevent investment in necessary infrastructure, limiting growth and leading to operational challenges.
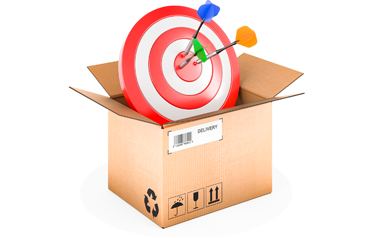
Desire to focus on core activities
Managing order fulfillment can divert attention from core business activities and negatively impact overall business development and growth.
Key Characteristics When Choosing a 3PL Partner
If several or more of the pain points described above apply to your company’s situation regarding order fulfillment, it may well be time to consider outsourcing to a 3PL provider or switching from one 3PL partner to another. Below are the key considerations to keep in mind when evaluating potential 3PL warehouse order fulfillment providers:
Why Choose IDS for Pick and Pack Fulfillment?
Now that you know the key factors to consider when searching for a 3PL warehouse and order fulfillment partner, here’s what we want you to know about IDS:
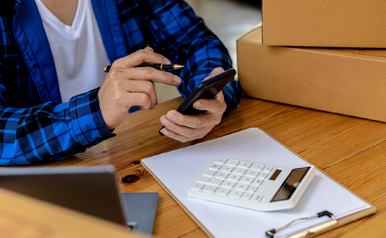
Cost
IDS relentlessly pursues continual improvement on efficiency, which can lead to cost savings. We are also transparent about our pricing, allowing your business to budget for fulfillment services accurately.
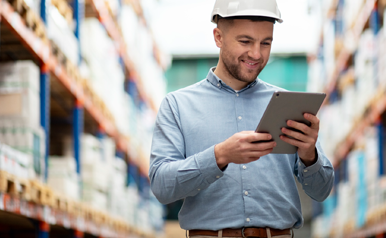
Technology and efficiency
We utilize advanced warehouse management systems, various picking methods to ensure efficiency and accuracy, and superior shipping software to obtain the optimal mix of cost and speed of delivery.
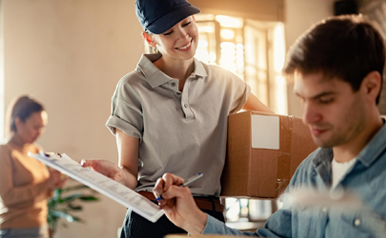
Customization and flexibility
IDS designs processes and procedures around individual businesses and products, ensuring a tailored approach to order fulfillment. Moreover, we offer flexibility across the board, including flex labor, integrated robotic systems, and the ability to add additional stations as needed, ensuring we can meet diverse business needs.
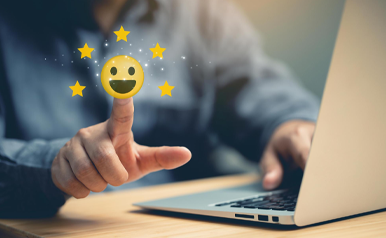
Reputation and reliability
IDS has a longstanding reputation for delivering superior third-party logistics services, supported by a wealth of experience in the industry that comes from more than fifty years of providing our clients with practical solutions.
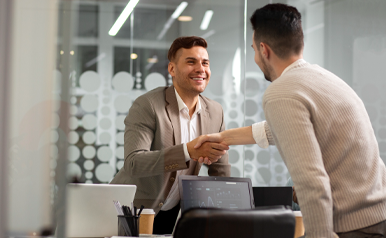
Customer support and communication
We always emphasize effective communication and reporting, allowing you to monitor and manage logistics operations seamlessly. IDS strives for excellence in customer support.
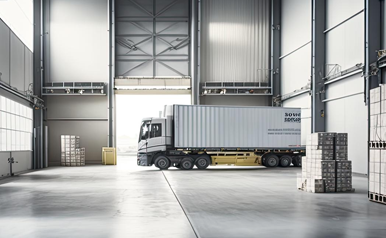
Location
Strategically located fulfillment centers, including the Crossroads of America (Indianapolis, Indiana), the Crossroads of the West (Salt Lake City, Utah), and the Southeastern Crossroads (Atlanta, Georgia) ensure both accessibility and efficiency in distribution.
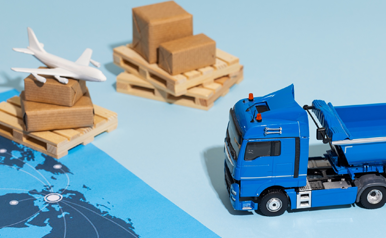
Scalability
IDS offers flexibility to meet your needs, including flex labor, integrated robotic systems, and increased staffing.
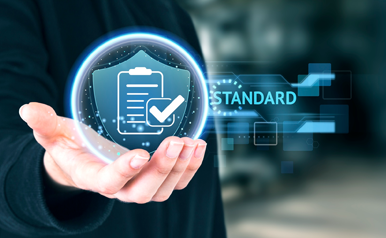
Safety and compliance
We’ve made safety and compliance an ongoing priority so our clients know we adhere to all applicable regulations and quality standards for the secure handling of various products and materials.
IDS Technology Advantage: Our Warehouse and Shipping Systems
It’s critical to emphasize the importance of technology to superior pick-and-pack order fulfillment. Our warehouse management system (WMS) drives IDS as a leader in the pick-and-pack order fulfillment industry. Designed to automate and optimize overall operations, the WMS keeps a live record of all inventory and orders, giving our clients real-time visibility to instantly find any order status and see what’s happening with their merchandise.
This system is also the key to maintaining accuracy, with employees updating each order at every step. It’s the WMS that allows us to focus on not only efficiency and accuracy but also scalability. Online ordering is a living ecosystem, fluctuating based on any given day or time of year. IDS offers flexibility across the board, including flex labor, integrated robotic systems, increased staffing, and the ability to add additional stations as needed. This allows us to provide top-level, white-glove service to our clients with minimal delays or disruptions. Read more about our Warehouse Manage System.
We’re also proud to give our clients access to the ProParcel shipping solution that cuts through the differences between carriers to accurately pinpoint and automatically select the most cost-efficient shipping carrier and shipping method for each order. The system is customizable to your preferences so you can meet your company’s customer expectations.